BY THE SUPERYACHT REPORT
Is it time for a technological re-evaluation of mooring operations? The team at Rondal certainly thinks so. Here, we speak with managing director Harald Lubbinge and technical product specialist Ard Ritsema about their innovative captive mooring and self-contained mooring winch system.
MODERNISING
MOORING OPERATIONS
The process of mooring is fundamental to maritime operations. It serves as the literal connection point with safe harbour, integral to peace of mind for operators and owners alike. It’s also one of the most dangerous hands-on operations on board.
As a large yacht is secured to a fixed dock, especially in high winds, deck crew are regularly handling large lines under enormous loads. Orders are barked across crowded radio channels, all with potentially dangerous consequences. Traditionally, this process is done using an array of deck capstans, elbow grease and thrusters. Once attached to the dock, these lines then need to be removed from the winch (capstan) that tensioned them and ‘bounced’ on to a bollard – mostly by hand.
Despite significant technological advancements across all aspects of onboard operations, mooring processes have remained a curiously analogue outlier. Checking the tension on lines is also primarily done visually. As tides and winds influence a yacht’s mooring, the safety of the vessel is gauged by eye and feel.
However, Rondal, a leading expert in custom captive winch design which has been producing captive winches for more than 30 years, is looking to modernise this aspect of deck operations by introducing a more advanced and safer mooring system for large motoryachts. The company’s track record speaks volumes: Juliet, delivered in 1993, was the first yacht equipped with Rondal captive winches. Remarkably, the original winches are still on board, a testament to their enduring reliability. Juliet’s captain, Jonathan Allan, confirmed they have undergone minimal servicing over the years.
These winches have been installed on a large number of sailing superyachts from various shipyards since their debut, and they have been continuously improved and developed over the years to become even better, ensuring unparalleled safety and efficiency in mooring operations.
“We had a motoryacht customer who saw our winches, which he had normally used for our sailing system, and he asked us if it could also be used for mooring,” says Rondal’s managing director Harald Lubbinge. “We were not specifically doing that at the time, but we had a meeting quite recently and have moved ahead to design a complete system.”
There is a regulatory catalyst for this development also. On 1 January, the International Maritime Organization (IMO) introduced revised SOLAS Regulation II-1/3-8 and associated guidelines aimed at enhancing safety and efficiency in towing and mooring operations. This update underscores the imperative for greater consideration of occupational safety and secure mooring when designing new vessels. As of 2024, mooring vessels more than 3,000gt will become a mandatory hands-off procedure, and for vessels of less than 3,000gt it’s strongly advised.
The amendments by the IMO Maritime Safety Committee emphasise key functional objectives for mooring systems, including minimising obstructed access, reducing manual handling and enhancing safety for personnel involved in mooring operations.
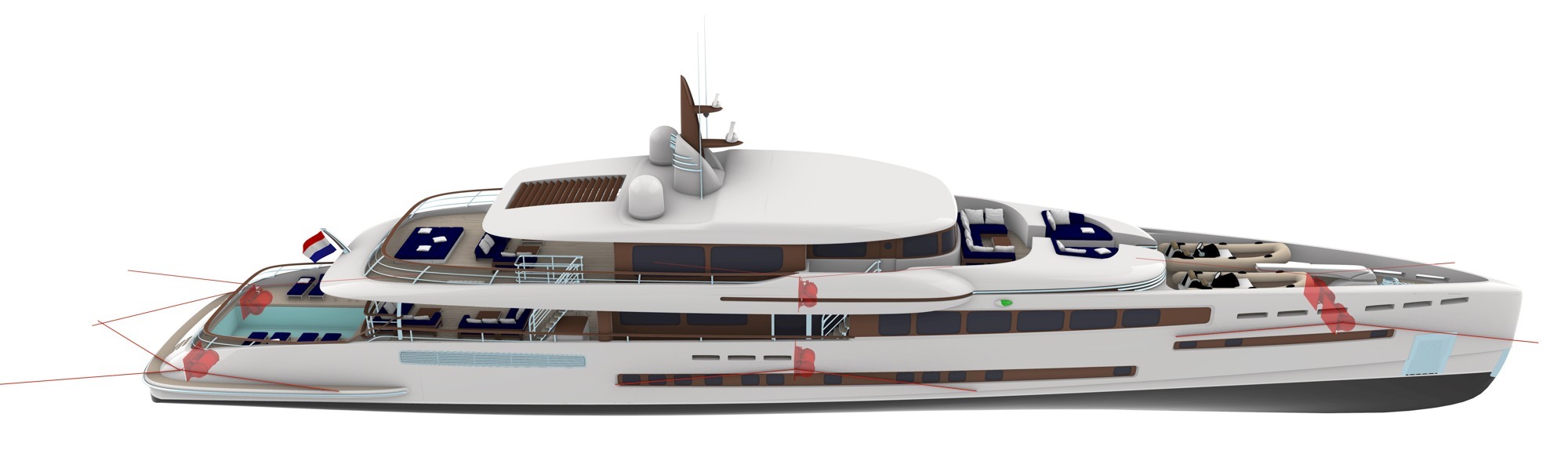
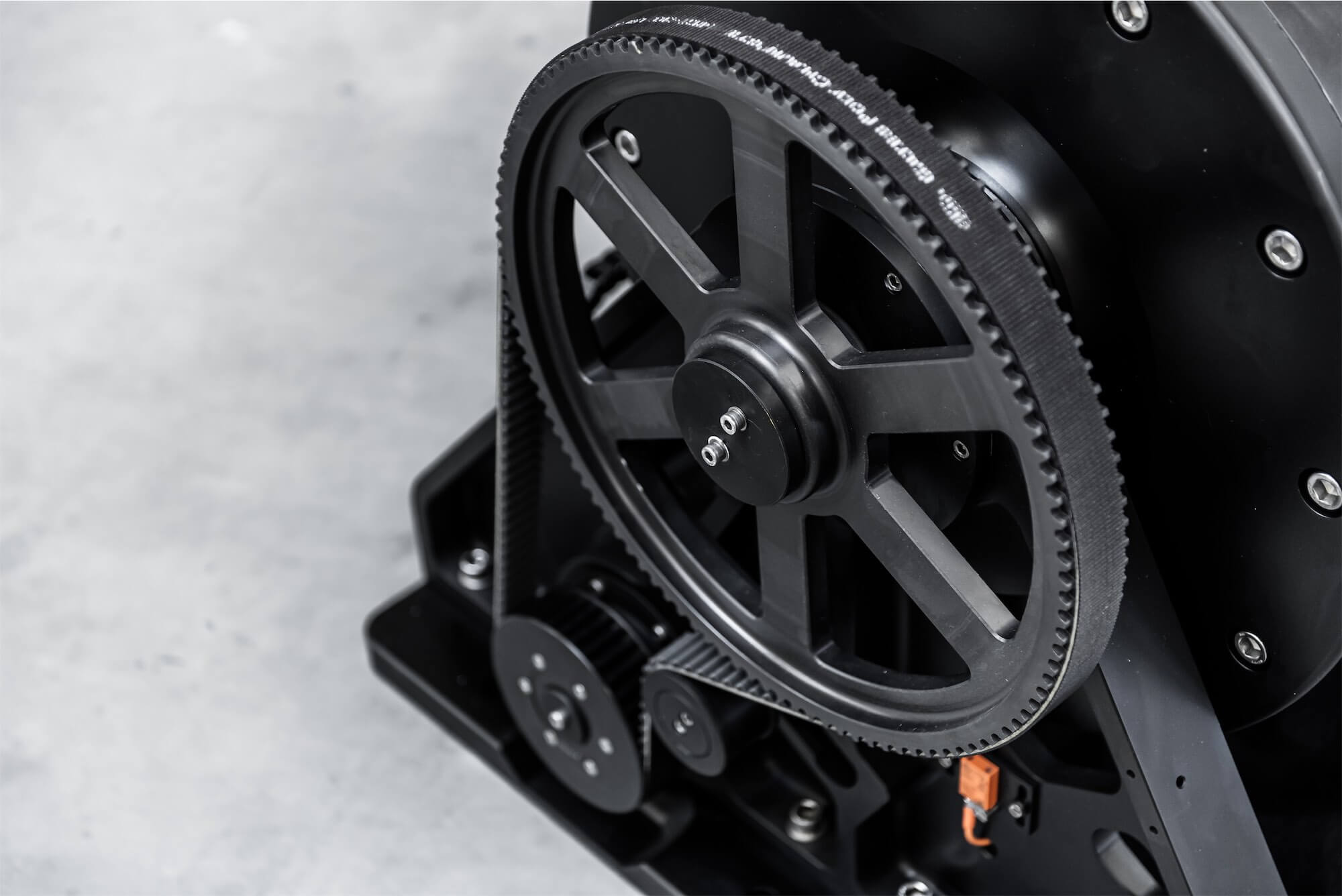
Above: Captive winch mooring systemn. Below: Rondal captive winch, demonstrating reliability and attention to detail. Photo: Tom van Oossanen
Rondal seeks to supply a complete mooring system that can integrate with yacht builders during the construction process. By focusing on the most efficient line running on board, whether electric or hydraulic winches, the system is designed to offer a more consolidated solution. When operating high loads entirely hands-free, it substantially reduces crew-safety risks and is cleaner and more precise. No cleating is required, and when trimming the mooring line, no manual line-handling is needed, therefore ensuring safety.
Two crewmembers, each with a local control unit, can split responsibilities for faster adjustment if preferred. Loads on all the winch sheaves are monitored and integrated with the ship’s AMS system. The system’s load capacities meet established classification requirements.
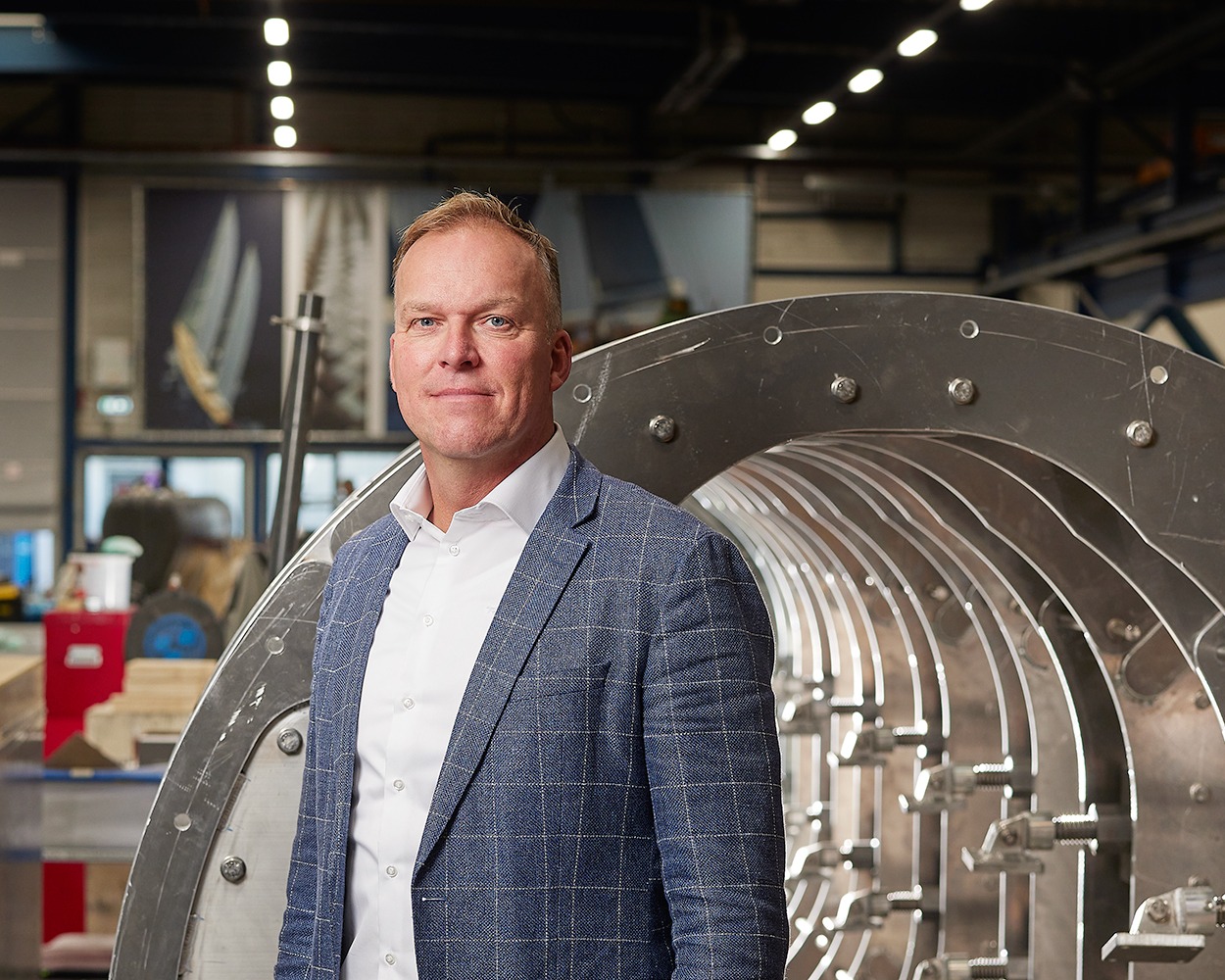
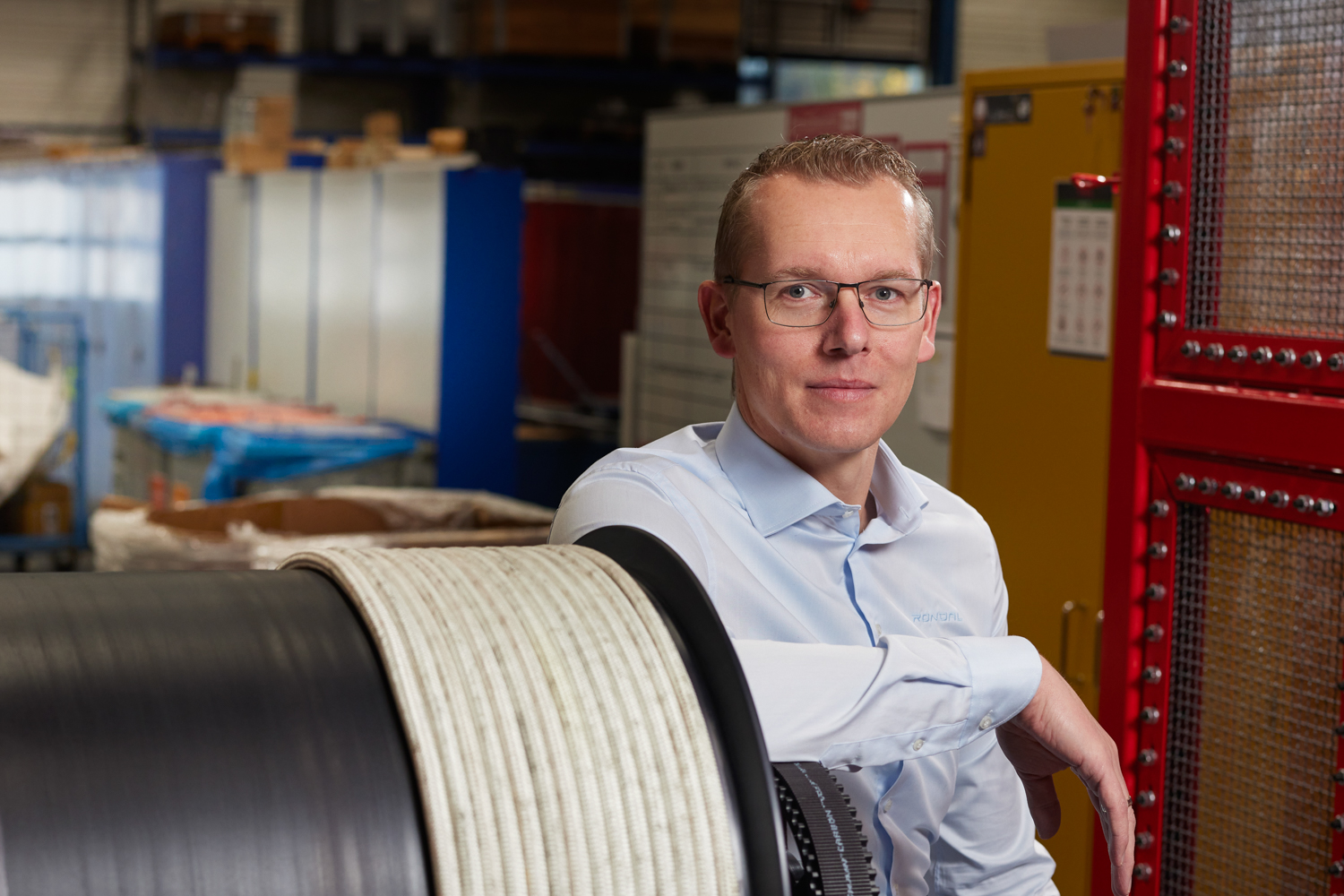
Above: Managing Director Harald Lubbinge. Below: Technical product specialist Ard Ritsema
By installing the winches below deck and controlling them remotely, the system minimises the risk to crewmembers and ensures a clean deck layout. Moreover, sensors on the winches continuously monitor tension levels, providing real-time alerts and ensuring optimal safety and efficiency during mooring operations.
Captive drum winches, as seen left, are staples of the large sailing-yacht fleet for managing rigging and are an alternative solution that can be applied to mooring operations. Rondal has pioneered a self-contained and selfflaking system for yachts in the past.
“Our winches have quite a long drum where we can store lines and also pull the lines as needed,” says Rondal technical product specialist Ard Ritsema. “Our current motoryacht client wanted to have those winches operated remotely to avoid the tension getting off to the drum. They saw the benefit of having the system be safer and less interference between the line and the crew.”
One of the significant challenges encountered in mooring operations is dealing with overruns and ensuring quick tensioning, especially when retrieving slack lines.
The primary advantage of this is that it allows deck crew to stand at a safe distance controlling the lines. A crewmember theoretically only needs to handle the line if tension needs to be adjusted. This will be done by remote control, with no physical interaction during mooring. A sensor warns if the line is over-tensioned or if there is slack line, and a crewmember will then adjust the tension in the line by remote control but, otherwise, they can be at a safe distance. This will hopefully make life a lot easier for mooring purposes.
“We have sensors on the winches that measure tension on the line. If there’s too much tension, the system sends a signal to the yacht’s control system,” adds Ritsema. “The control system can then take action, such as adjusting the tension or alerting the crew if needed.”
To have such capability would be advantageous and a break from tradition. As any deck crew can attest, manhandling heavy lines under tension is a stressful side of operations. Any system would need to have a lot of strength in the drum and its attachment point because it would be handling huge loads, which is why this system is fully integrated into the build process.
“The regulations have become stricter, especially for vessels above 3,000gt, where mooring systems are becoming mandatory,” says Lubbinge. “For vessels below 3,000gt, it’s highly advised to ensure safety and compliance with regulations. We want to continue to discuss further with classification societies how they see our system’s application over a wider range of the fleet.”
One of the significant challenges encountered in mooring operations is dealing with overruns and ensuring quick tensioning, especially when retrieving slack lines. However, Rondal’s system includes tensioners and sensors to detect slack lines and automatic tensioners to prevent such issues, thereby mitigating operational challenges. The tensioners avoid slack line on the drum of the winch but if there’s a slack line between the yacht and the quay, the line can be tensioned by remote control.
Due to the wide range of available captive winches, the Rondal mooring system can benefit yachts of various sizes; larger motoryachts of 60 metresplus, with more space and heavier loads, stand to gain significantly from the added safety and automation. Additionally, compliance with stricter regulations, especially for vessels more than 3,000gt, further emphasises the importance of adopting innovative mooring solutions.
With encroaching regulations seeking to address a historically dangerous aspect of deck operations, a more technologically advanced and handsfree system presents an intriguing option for new builds. As the Rondal team, – as well as the regulations – lay out, this is likely to be employed by the 3,000gt-plus fleet initially, but with advancement in line technology, it may also be feasible for smaller yachts.
“Convention has dictated that we do it a certain way for centuries,” concludes Lubbinge. “But it may be time to bring this aspect of operations into the next generation.”